Maximizing Quality: Overcoming Die Casting Defects
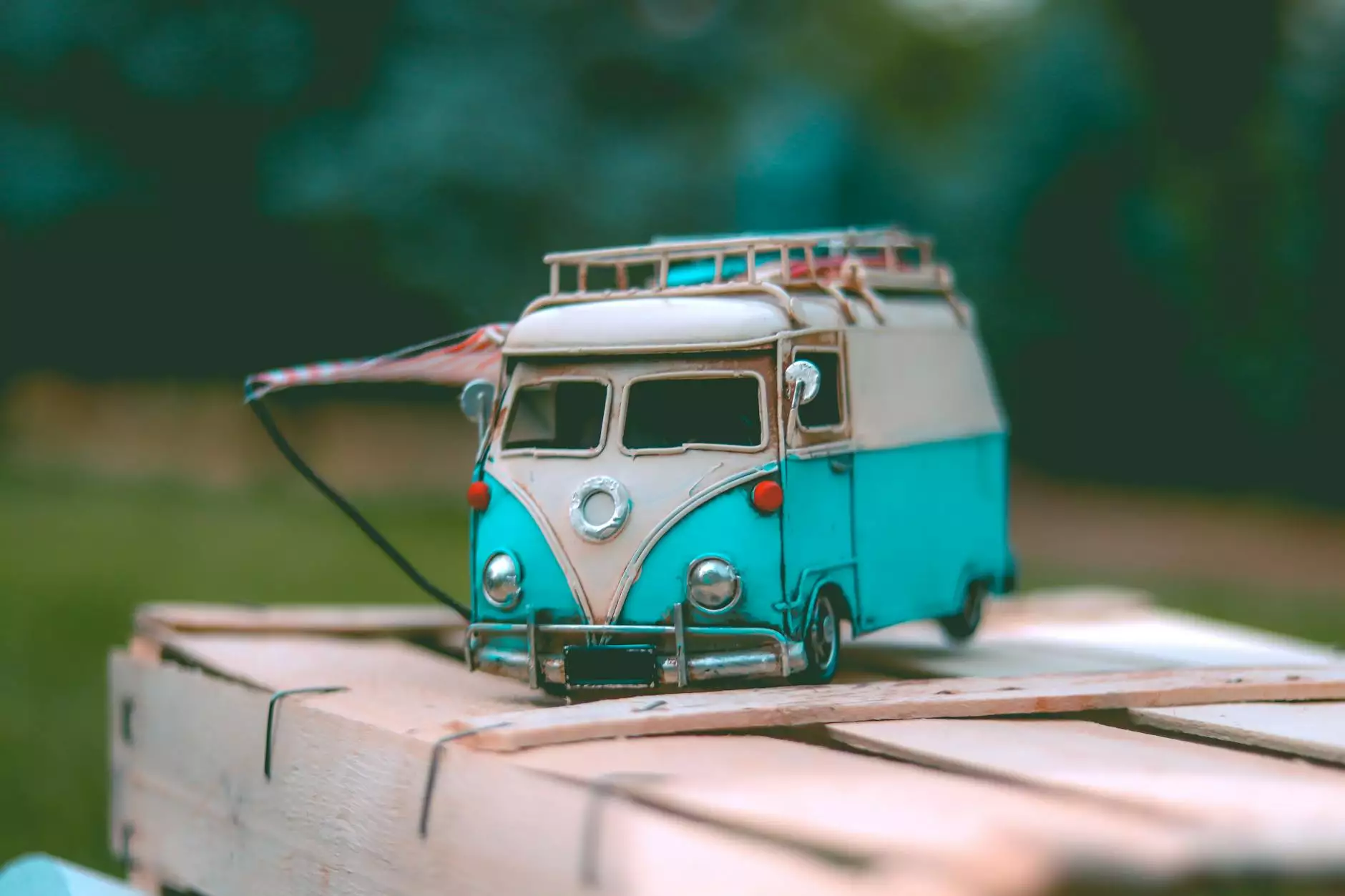
The Art of Manufacturing
Wetron Industrial is a leading company in the Home & Garden appliances industry, known for its unwavering commitment to quality and innovation. With years of experience and a team of dedicated professionals, Wetron Industrial has established itself as a trusted brand for customers worldwide.
Understanding Die Casting Defects
In the world of manufacturing, die casting is a widely used process for creating intricate and complex metal parts. However, like any other manufacturing method, it is not immune to defects. Die casting defects can range from minor imperfections to critical flaws that affect functionality and overall quality.
At Wetron Industrial, we understand the importance of producing flawless products. Our team of experts constantly strives to overcome die casting defects and deliver exceptional appliances to our customers. We believe that attention to detail and continuous improvement are key to ensuring the highest level of quality.
Common Die Casting Defects
Porosity
One of the most common die casting defects is porosity. This occurs when tiny air pockets form within the casted part, leading to weakened structural integrity. At Wetron Industrial, we tackle porosity by employing advanced quality control measures. Our state-of-the-art equipment and meticulous inspection processes help us identify and rectify any porosity issues, ensuring that our products are strong and durable.
Shrinkage
Shrinkage is another challenge in the die casting process. It happens when the material undergoes volume reduction while cooling, resulting in visible defects such as voids or distortion. Wetron Industrial has developed innovative techniques to counteract shrinkage defects. Through precise control of casting temperatures and the use of high-quality alloys, we minimize shrinkage and maintain the dimensional accuracy of our appliances.
Cold Shutdowns
Cold shutdowns occur when molten metal cools too quickly during the casting process, leading to incomplete fillings or weak spots. To address this, Wetron Industrial employs advanced software simulations and molds designs that optimize the flow of molten metal. By ensuring consistent, controlled cooling, we prevent cold shutdowns and produce flawless parts every time.
Continuous Improvement: Our Commitment to Excellence
At Wetron Industrial, we believe in constant improvement. We embrace a culture of innovation and invest in cutting-edge technologies to stay ahead in the industry. Our R&D team works tirelessly to explore new materials, refine manufacturing processes, and enhance product performance.
We also nurture a strong partnership with our suppliers, carefully selecting those who share our commitment to quality. Our stringent supplier evaluation process ensures that we receive only the best materials and components, further enhancing the reliability and durability of our appliances.
Conclusion
When it comes to overcoming die casting defects and delivering top-notch Home & Garden appliances, Wetron Industrial sets the standard. Our dedication to quality, meticulous attention to detail, and relentless pursuit of excellence make us a trusted choice for customers worldwide.
Choose Wetron Industrial for unparalleled quality and performance. Experience the difference today!