The Science of Die Casting Defects and Prevention
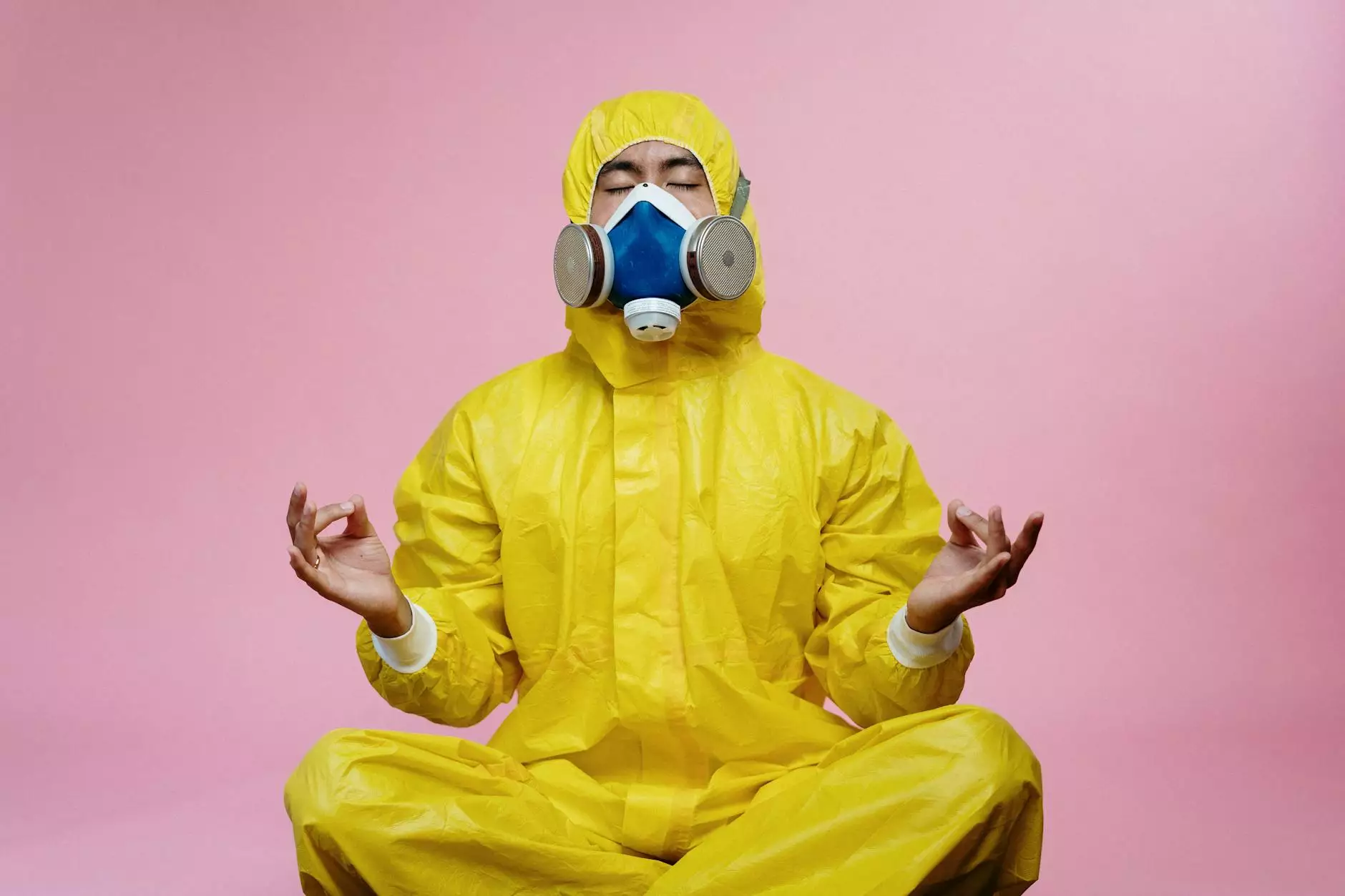
As a reputable manufacturer of high-quality home and garden appliances, Wetron Industrial understands the importance of delivering flawless products to its customers. One critical aspect that directly affects the quality of our appliances is the die casting process. In this article, we will explore the science and mechanics behind die casting defects and provide valuable insights on how to prevent them.
The Basics of Die Casting
Die casting is a manufacturing process used to shape molten metal into intricate and accurate designs. It involves injecting molten metal, typically aluminum or zinc alloys, into a reusable mold called a die. The molten metal rapidly solidifies within the die's cavity, resulting in precise and complex parts with exceptional strength and durability.
However, despite its numerous advantages, die casting is not immune to defects. Understanding these defects and their underlying causes is vital to ensure the production of high-quality appliances.
Common Die Casting Defects
1. Porosity: Porosity refers to the presence of small voids or gas pockets within the cast part. It is commonly caused by trapped air or gas during solidification. Porosity can compromise the structural integrity and aesthetics of the final product.
2. Cold Shut: Cold shut occurs when two or more streams of molten metal do not merge completely, resulting in an incomplete fusion. This defect manifests as visible lines or gaps on the surface of the part.
3. Shrinkage: Shrinkage defects happen when the metal contracts during solidification, causing voids or shrinkage cavities. These defects can weaken the part and compromise its functionality.
4. Flash: Flash defects occur when excess molten metal escapes from the mold cavity, resulting in thin excess material or fins along the parting line. If left unaddressed, flash can impair the efficiency and performance of the product.
Preventing die casting defects requires a systematic approach, involving careful design, process optimization, and quality control. Wetron Industrial follows industry best practices to minimize the occurrence of defects and deliver superior appliances.
Preventing Die Casting Defects
1. Proper Mold Design: Successful die casting starts with the right mold design. Factors such as gate and runner placement, venting, and cooling channels significantly influence part quality. By optimizing the mold design, we ensure proper filling and cooling of the molten metal, leading to defect-free products.
2. Alloy Selection and Optimization: Choosing the right alloy composition is crucial for achieving optimal die casting results. Wetron Industrial carefully selects alloys with ideal fluidity, thermal conductivity, and mechanical properties to minimize the risk of defects and enhance the performance of our appliances.
3. Process Control: Implementing stringent process control measures ensures consistent and reliable production. Monitoring key parameters like temperature, pressure, and injection speed helps us identify potential defects early in the casting process, allowing for corrective actions to be taken promptly.
4. Quality Assurance: At Wetron Industrial, we prioritize quality at every step. We conduct thorough inspections, including visual checks, dimensional measurements, and non-destructive testing, to guarantee that only defect-free parts make their way to our customers.
By following these preventive measures and continuously improving our processes, Wetron Industrial maintains its position as a leader in the production of top-notch home and garden appliances.
Conclusion
Die casting defects can be detrimental to the overall quality and performance of manufactured products. Wetron Industrial's commitment to excellence drives us to constantly refine our die casting processes, eliminating defects and providing customers with reliable, durable, and aesthetically pleasing appliances for their home and garden needs.